DC250 style
For Xerox® models: (DocuColor) DC-240, 242, 250, 252, 260 (WorkCentre) WC-7655, 7665, 7675, 7755, 7765, 7775 & Xerox® Color 550, 560, 570, C60, C70, (Digital Color Press) DCP700, DCP700i, DCP770, C75, J75, (PrimeLink) C9070, C9065

The first time we looked at one of these fusers was in an ENX article in early 2009. I found the procedure to be relatively involved and time consuming, but still well worth the effort. Well… recently a technician who I know and respect mentioned that this fuser was “easy” to rebuild… and he told me he has gotten so good at these, that he can rebuild one in ten minutes flat. That was amazing to hear… I thought maybe he was getting confused with some other fuser. He explained that he opens the fuser like a clamshell. I missed that back in 2009, so I think that it’s time to revisit the rebuild procedure on this extremely popular series of fusers. Let’s have another look… at an easier way to approach it.
FUSER REBUILD PROCEDURE:
1. Start with the Top Cover… (2 screws on top from above, and 2 screws near the right side, also from above) (3mm short screws… 5.5mm hex, or #2 phillips driver). This gives you easy access to both the Thermostat and the Fuser Reset Fuse as well as the thermistors (see Photo 1). The Thermostat is can-shaped and in-line with the fuser heat lamp circuits. The Fuser Reset Fuse is a standard bullet-shaped thermal fuse. When replaced, if you run 50 copies or more, the fuse gets hot enough to blow, at which point the machine will reset the Fuser Life to 100%.
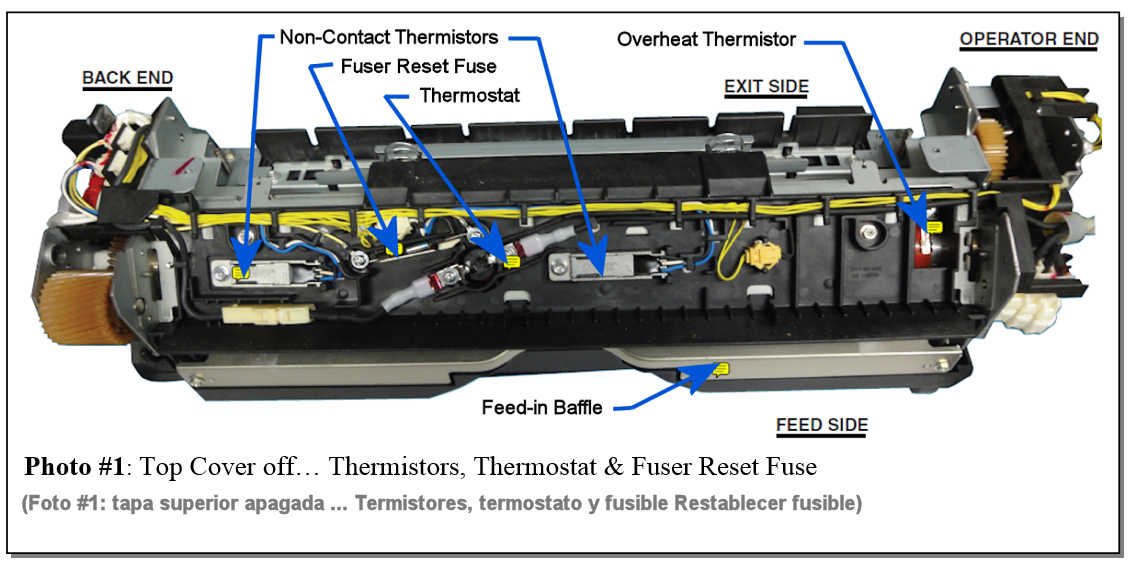
2. Remove the Front End Cover (2 screws from the front)…which exposes the pressure gear / cam mechanism and its home sensor (see Photos 2 & 3).
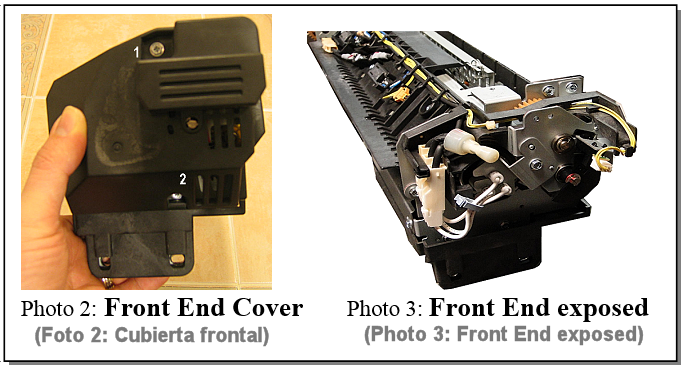
3. Remove the Rear End Cover (2 screws from rear, see Photos 4 & 5).
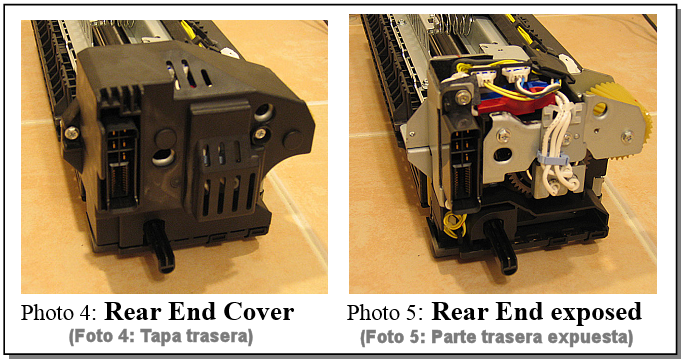
4. Remove the Lower Fee-in Baffle (metal baffle, refer back to Photo #1).
5. Disconnect the 3 front heat lamp terminals & remove the front heat lamp holder bracket (1 screw)… note: do not remove the shoulder screw at the upper right corner as that is the pivot point for opening the clamshell later.
6. Disconnect the 3 rear heat lamp terminals & remove the rear heat lamp holder bracket (1 screw) (see Photo #6). Note: Don’t remove the shoulder screw at the upper left corner.
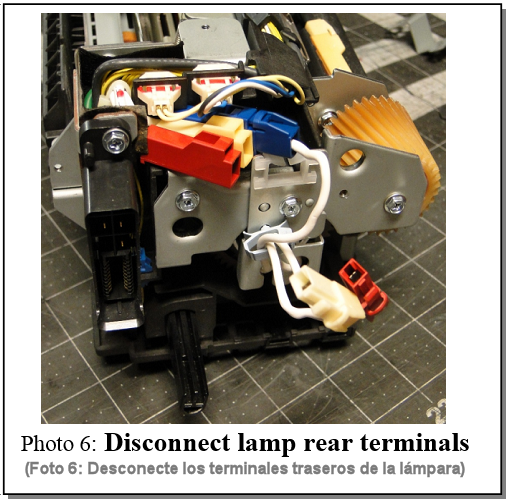
7. Carefully slide each of the heat lamps out one at a time. Be very gentle.
8. Disconnect the blue connector for the Exit Switch at the back end (3 yellow wires).
9. Measure the height of the Pressure Screws so you can return the pressure to the same position later (see Photo #7). Then back out both pressure screws.
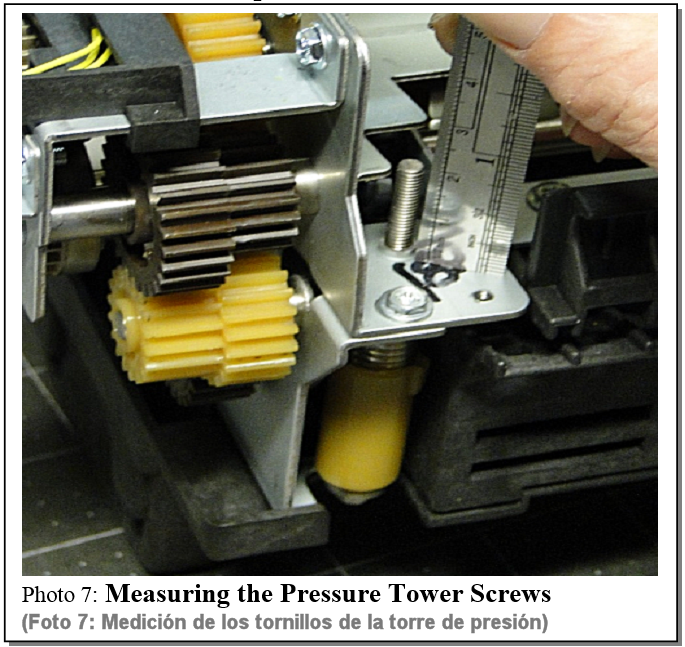
10. Next remove the two screws which secure the top clamshell closed to the bottom frame (see the screw next to the ruler and the pressure screw shown in Photo #7)
11. Now raise the upper half of the fuser, it will pivot on the two shoulder screws and open like a clamshell (see Photo #8).
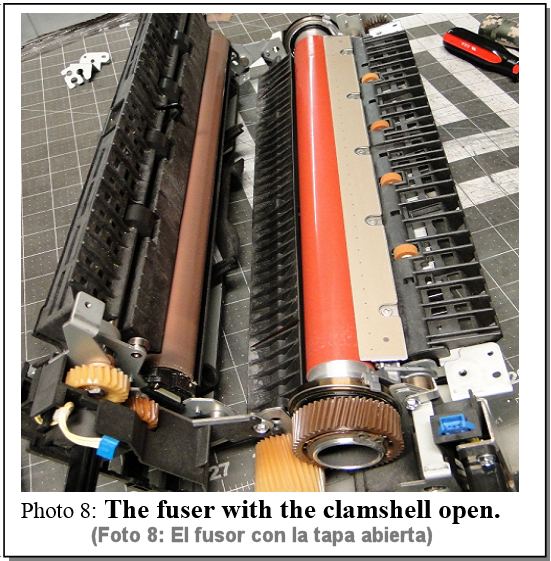
12. Loosen the screws for the Heat Roll Bearing retainers (these are little metal angled pieces which hold the bearings in place). Pivot the bearing retainers away from the heat roll bearings. (see Photo #9)
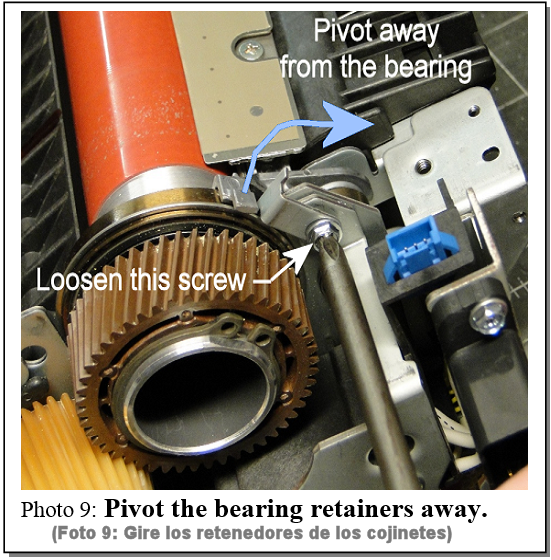
13. Next you’ll need to pivot the Stripper Plate away from the heat roll. It’ll help if you first pivot the black plastic exit baffle down a little to give you more room to move the Stripper Plate. Be gentle here, you don’t want to bend anything out of shape. Then lift the Heat Roll assembly out of its cradle. Clean the edge of the stripper plate gently (with something no harder than your thumbnail) to remove any baked on toner or other debris.
14. From the old heat roll, remove the snap-rings (you’ll need snap-ring plyers here) and move all of the hardware over (gear, bushings, bearings and snap-rings) over to the new heat roller. If the bearings are not moving smoothly replace them.
15. Install the new heat roll with something between its surface and the stripper plate for protection (for example the foam sheet the new heat rolls come wrapped in, or a piece of heavyweight cardstock). Make sure the bearing flanges are positioned properly to the outside of the metal frame on both ends and then pivot the bearing retainers so they hold the bearings firmly once again, and tighten the screws which hold them (refer back to Photo #9)
16. Check the gap between the Heat Roll Stripper Plate and the heat roll’s surface. There are 5 set-screws along the length of the Stripper Plate with springs underneath. Gently and gradually adjust each screw in the row till the gap is narrow but so that the blade will not come in contact with the heat roll. The gap should be consistent from end to end. Too close and it could damage the heat roll, too far and paper jams will result more frequently with the paper finding its way under the stripper plate. You can use a single piece of 80 lb. cardstock as your gauge (see Photo #10). Note that the OEM fusers often have a larger gap than what’s good for them. My good technician friend told me that he’s in the habit of opening up the brand new fusers to reduce the gap before use.
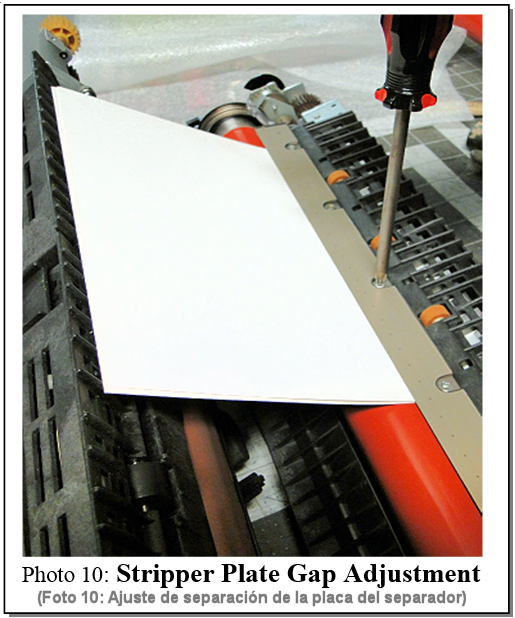
17. Next you can lift the Pressure Sleeve Assembly out (it has metal hooks which pivot on metal studs. Unhook it and gently lift it out of there (see Photo #11)
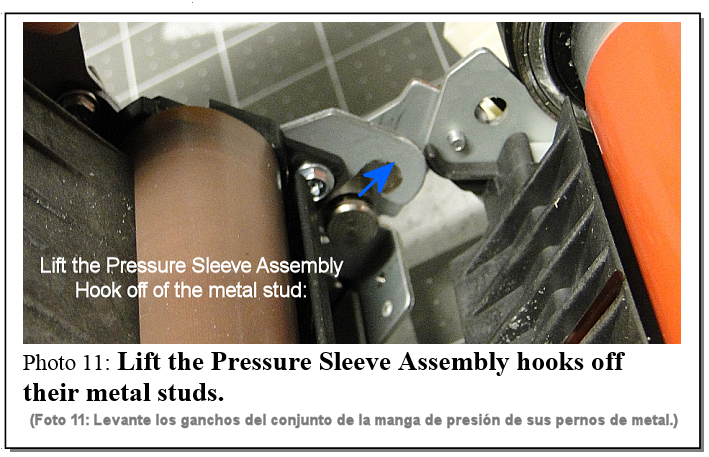
18. If the Pressure Sleeve is heavily worn or damaged, replace it. Remove one end plate, slide the sleeve off. When you go to reinstall the new sleeve, it helps to press on the sleeve a little right where the orange silicon pressure pad is (see Photo #12 & 13). This will help make the Pressure Sleeve the right shape for the end hubs to slip on without getting hung up on the edge of the sleeve.
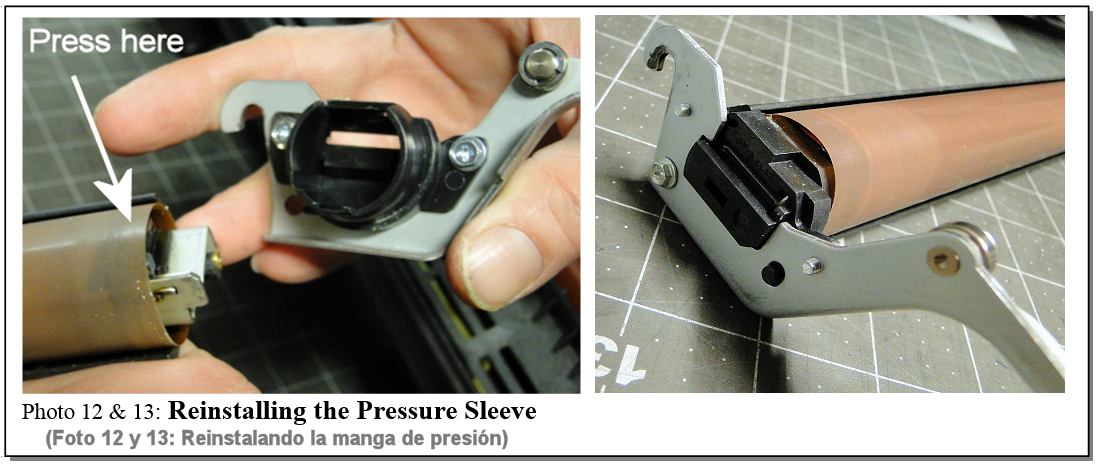
19. Now you can put it all back together again. Here are a few things to watch out for and to remember during reassembly:
- Once the pressure sleeve assembly is back in place, pivot the clamshell closed again carefully and reinstall the two retaining screws which hold the top frame to the bottom frame. Then turn the unit over and reinstall the two Pressure Tower Screws to the original height (approximately 18 mm).
- Be sure to reconnect the blue connector with the 3 yellow wires. (easily forgotten)
- Clean the heat lamps with isopropyl alcohol before reinstalling them and make sure not to get any fingerprints on the lamps or they’ll burn out very quickly. Pay attention to how the lamps sit into their brackets as you insert them. In particular watch at the Rear end where the lamps are differentiated by the colors of their terminals (Red, White & Blue). The Red and White have the same size ceramic ends, but if you look closely, you’ll find the bracket is marked with clues as to where each lamp belongs (see Photo # 14). If you look closely, there’s an “R” stamped in the metal where the lamp with the red terminal goes, & a “W” for the lamp with the white terminal.
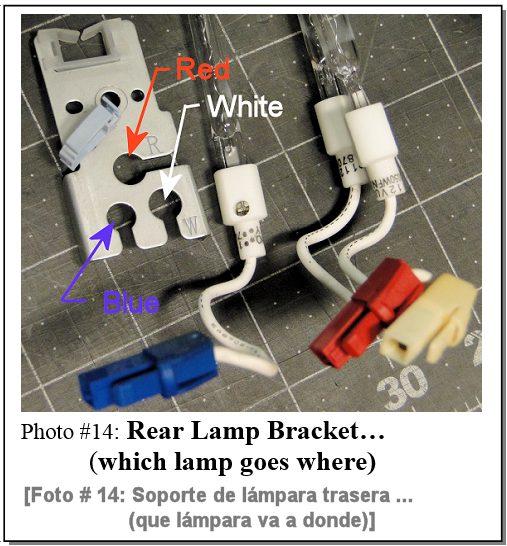
|